3D Printing Ushers in a New Age for Prototyping
Published by John Sembrot,
3D Printing Ushers in a New Age for Prototyping
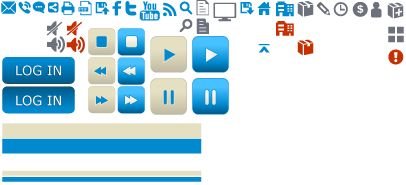
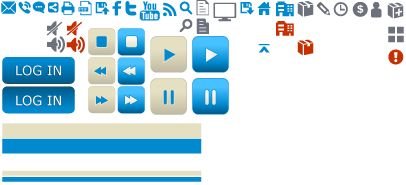
By providing engineers with a physical sample of a part or device design, prototypes offer a glimpse at the final look of a product. They enable someone to handle the design, get an idea of weight and “feel," use for evaluating packaging options, and give end users an opportunity to offer insights on potential improvements. While design simulation software is quite powerful, these are all benefits still realized through the use of actual physical prototypes, making them invaluable in the development process.
With 3D printing, the benefits realized from a physical prototype are even greater as the speed at which these can be provided is unlike anything previously available. 3D printed parts can often be turned around in 24 hours through a service provider or for those designers who have the luxury of their own printer in-house, they can get a physical prototype even quicker.
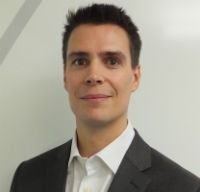
Simulation vs. Physical
Offering a brief insight on the value of both the physical prototype and the simulation, Clive Nicholls, product design and development manager at Owen Mumford, says, “Having a physical representation quickly is the ultimate goal to assess the form and function. And while simulations are no substitute for prototypes, they are hugely helpful in understanding risk and facilitating the comparison of changes to design geometry, as well as materials selection in static and dynamic environments."
Adding to the “support" for the physical prototype, R. Scott Rader, Ph.D., head of medical solutions at Stratasys Ltd., says, “Physical prototypes can show the effect of real-world inhomogeneity of materials, allow physical testing of complex loading through physiologic structures that are hard to model in simulation software, and are required along the validation path. Physical prototypes allow non-engineers and engineers alike to subjectively test physical products for important parameters we have not learned how to program into simulation software."
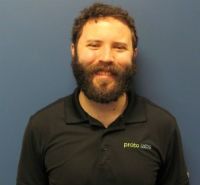
Jumping off from the mention of “non-engineers," Eric Utley, applications specialist at Proto Labs, expands on this aspect with his own comments about how physical prototypes help in gaining valuable insights from medical professionals who will ultimately use the device. “Especially with medical devices, a physical part demonstrates the weight and feel of the device in-hand. Also, the physical part can then be given to surgeons or other users for design feedback. The physical part can be used in a lab or simulation to evaluate the effectiveness."
Perhaps putting the most insightful spin on the value of the physical prototype, Danius Silkaitis, a senior manufacturing engineer at Stratos, says, “Prototyping is absolutely critical for verification of design and assembly. There is inevitably an unforeseen issue despite being able to inspect a design through software. Much like the saying, ‘a picture is worth a thousand words,’ a prototype is worth a million words to a development team."
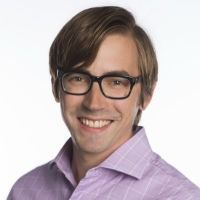
Materials
There was a time when 3D printing was performed rapidly, but only in one color or with very few types of materials. This revolutionary process has quickly advanced beyond those limitations. Today, many different types of materials are available for 3D printing prototypes (also offering multiple materials at the same time for different aspects of the device). With this also comes a rainbow of color choices, enabling end users to not only get the weight and “feel" of the device, but the aesthetics as well, which is certainly becoming a critical element in medical device design.
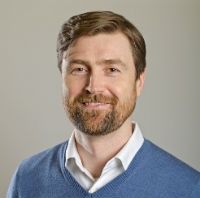
“Historically, materials allowed for the creation of parts that were either robust or precise, but balancing the two in an engineering material capable of being 3D printed was difficult," explains Sean Corrigan, director of engineering at Insight Product Development. “Today's materials are capable of withstanding very high temperatures, are biocompatible, or are extremely mechanically tough. This evolution in the material properties available allows for prototypes to be created that not only represent the intended geometry, but the intended engineering function. Rather than simply performing fit checks, engineers can run functional tests."
Expanding further on this, José Wong, vice president of engineering and program management at Farm Design Inc. offers insights on material options that may be most interesting for medical device developers. “DMLS material options are available that can be used for production applications ranging from medical imaging to implantables. These materials are of high quality, high accuracy, and reduced porosity, and accommodate post-machining if needed." Continuing on about other material options, Wong says, “Biocompatible SLA materials have been a big innovation as well. Suppliers are able to supply prototypes that can ultimately be used in clinical trials."
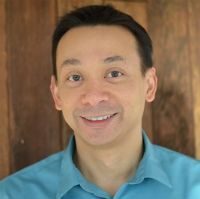
What’s Ahead?
While it’s already become an incredibly valuable tool in product development and specifically, the production of physical prototypes, 3D printing is still essentially in its infancy. It has not been available to most for very long and certainly not compared to other component fabrication methods. That said, it has an incredibly bright future and its use will likely grow exponentially in medical device development as well as across virtually every other manufacturing industry. The roundtable participants offered their own insights on what can be expected from this exciting technology.
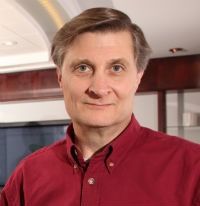
“Within five years, 3D printing will probably be capable of producing parts that are very close to production-ready, making the medical device development process much quicker," says, James VanderWende, GW Plastics healthcare engineering manager. “Within 10 years, it will probably be capable of taking over low volume production entirely."
David Foshee, a senior level engineer at EG-Gilero predicts that “materials in SLA will continue to improve incrementally. The resolution of 3D printers will improve and with that, the surface finishes it produces. It would be cool if you could print electronic elements into a build so that they would be embedded in the end product. The most incredible advances would be in tissue printing if they can get to the point of making implantable organs."
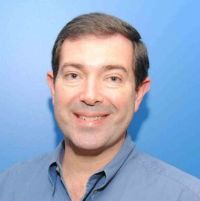
“We're already seeing the beginning of the development of devices customized to each individual patient. 3D printing is used in the rapid production of custom dental implants and prosthetics, as well as in tools and templates to make conventional orthopedic procedures faster and less traumatic," says Corrigan. “This trend will continue over the next decade and has the potential to further reduce both the time it takes to commercialize devices, as well as the time it takes to bring the benefits of those devices to individual patients that need them."
“As knowledge of the technology grows among engineers and medical device designers, the applications will explode," predicts Utley. “3D printing will continue to be the go-to technology for rapid prototyping. There will be more personalized, production 3D printed devices that conform to the specific patient. The use of direct metal laser sintering will grow for creating customized metal components, or highly complex metal components for low volume devices."
Regardless of anyone’s specific expectations of 3D printing technology, whether for prototype parts or for final production ready components, this capability promises to make an even more dramatic impact on the medical device space.
Entries Open: Establish your company as a technology leader. For 50 years, the R&D 100 Awards, widely recognized as the “Oscars of Invention," have showcased products of technological significance. Learn more.
Share this Story
Comments

Also on Medical Design Technology
Government Maps Out Interoperability Plan for EHRs
- 1 comment •
- a month ago
Paul Fred Frenger — Interoperability: great idea! So why was this issue not addressed before the government …
Anxiously Awaiting a Device to Calm Down
- 1 comment •
- 6 days ago
Mark Strong — I have had a "calm down" device for decades. It's called a martini shaker
First 'Made for iPhone' Custom Hearing Aid
- 4 comments •
- 22 days ago
Sean Fenske — Noooooo, that couldn't be true! <heavy sarcasm="">
Creating Cartilage from Stem Cells
- 1 comment •
- 20 days ago
rhansing — could be a game changer...
Search form
3D Printing Ushers in a New Age for Prototyping
March 24, 2015 10:49 am | by Sean Fenske, Editor-in-Chief, @SeanFenskeImproving Cellular Response to Intervertebral Fusion Surgery Materials
March 24, 2015 8:40 am | by Peter Ullrich, CEO, Titan SpineNew Surgery Simulators Made by 3D Printing Pioneers
March 23, 2015 3:46 pm | by Megan Crouse, Real Time Digital Reporter, @abmdigiHow to 3D Print Metal Teeth
March 23, 2015 12:03 pm | by Megan Crouse, Real Time Digital Reporter, @abmdigi- First Engineering-Based College of Medicine
1 comment · 1 day ago
- MDT Live Preview: The Impact of 3D Printing on Healthcare
3 comments · 1 day ago
- Anxiously Awaiting a Device to Calm Down
1 comment · 5 days ago
- Rebooting the Healthcare System
3 comments · 1 week ago
- Don't Make the Same Mistakes in Device Design
1 comment · 5 days ago
Newsletters
- In Vitro Diagnostics News
- Highlights the latest trends, technologies, and news relevant to the in vitro diagnostics industry.
- MDT Daily
- News, technology, and product developments focused on medical devices and design.
- MDT Today
- A late-day update on breaking news in the medical design industry.
- MDT Technology & Video Showcase
- Products and technologies for the medical design market.
Our Partner Sites
Advantage Business Media © Copyright 2015 Advantage Business Media
http://www.mdtmag.com/articles/2015/03/3d-printing-ushers-new-age-prototyping